Cone Table Densification System
Cone table densification is designed to:
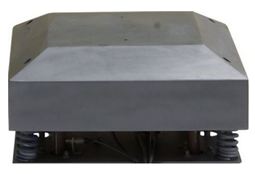
• Increase bulk bag stability
• Reduce bulk bag size/increase payload.
• Increase bulk bag filling throughput.
Cone Table Densification - How It Works
The cone table performs four functions:
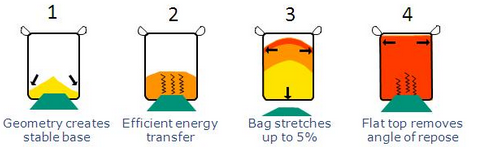
The primary objective when filling a bulk bag is to produce a stable and safe package. This is achieved when the product is densified to its packed bulk density while in the bulk bag filler, the bag is stretched during filling and the product's angle of repose has been flattened. The primary objective is more critical - and more difficult to achieve - as the filling rate increases.
The following cone table functions ensure that the primary objective is met:
1. Build stable base. The cone table's shape directs product to the bottom corners of the bag to create a stable foundation.
2. Transfer maximum energy. Because a pallet is not in the way the cone table makes direct contact with the bag resulting in maximum vibration energy transfer.
3. Stretch bulk bag. A bulk bag typically spends 50% of the filling cycle hanging from its loops and not in contact with the cone table. During this time the bulk bag stretches increasing volumetric efficiency and assisting with bag stabilization. A stretched and densified bulk bag will not slump and will hold more product.
4. Flatten angle of repose. Almost any dry bulk solid has an angle of repose - the angle formed by the peak of material produced when pouring a dry bulk solid. To produce a flat-topped bag, the horizontal top of the cone table pushes up a column of product every time it comes in contact with the bag. When the cone table is removed from contact with
In the below video watch the product drop and air boil from inside the bag showing the maximum vibration energy transfer of the cone table and its ability to densify even the most aerated products.